Customer Advisory – Cargo Operation Circular – Flat Rack Container Acceptance
Customer Advisory – Cargo Operation Circular – Flat Rack Container Acceptance
30/09/2023
Customer Advisory
Cargo Operation Circular Ref No. CMSWM0392017 (Ver.4)
Flat Rack Container Acceptance
Cargo shipped using flat rack containers must be properly stowed and secured to comply with applicable international & national regulations, including the IMO/ILO/UNECE Code of Practice for Packing of Cargo Transport Units (2014) and IMO Cargo Stowage & Securing Code.
In view of the above,
- The cargo payload must be homogeneously distributed over the loading floor. Concentrated load should be expanded by bedding on longitudinal H-beam girders. It may be necessary to transfer the weight to the corner posts by supporting the cargo on strong timber or steel beams as appropriate.
- The cargo should be so arranged that its centre of gravity is closer to the mid-length and mid-width of the flat rack container.
- Cargo packed on the flat rack must not obscure the top corner castings, and where the flat rack is required to be loaded underdeck in cell guide holds, the cargo and respective blocking/bracing materials should be stowed within 30cm of the corner posts of the flat rack,
For securing cargo units, strong lashing rings & brackets are to be welded to the outer sides of the longitudinal bottom H-Beam Girders with a Maximum Securing Load (MSL) of at least 30 kN according to the standard and also have additional lashing points with MSL of 50 kN and 100kN.
• All lashing materials must be of an approved type and suitable size and capacity, considering the weight of cargo to be secured.
• There must be a balanced number of lashings on each side of the unit, and lashings should be made up comprising the same components so that they have the same elasticity.
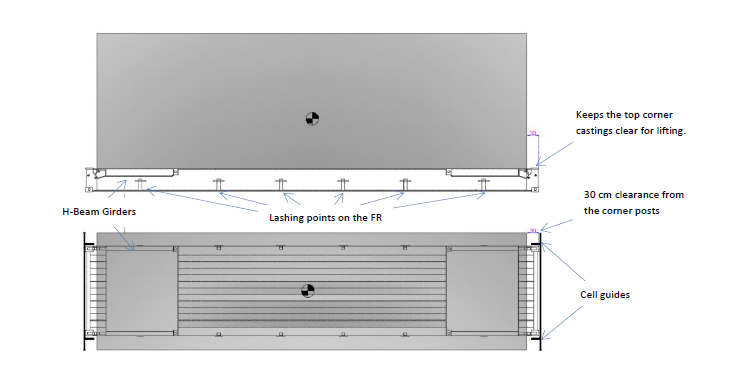
As a rule of thumb, the total of the Maximum Securing Load (MSL) values of the securing devices on each side of the unit of cargo (port and starboard) should be equal to 2.5 times the unit’s weight.
A combination of the “preferred lashing method” (see Annex 1) must be taken against longitudinal and transverse sliding & tipping forces.
➢ Direct Lashing: Prevents sliding and tipping but requires strong securing points on the cargo unit.
➢ Loop Lashing: Prevents transverse sliding and tipping but to be used in pairs.
➢ Spring Lashing: Prevents longitudinal sliding and tipping.
➢ Top Over Lashing: Increase friction only (to be used minimum for sea carriage)
Cargo may also be secured in the longitudinal direction by shoring to the end walls of the flat rack.
- Suitable “chafing gear” and “softeners” must be fitted on the lashings in any areas where the lashings make contact with the cargo, other lashings, or the structure of the flat rack itself to prevent damage or excessive wear and subsequent failure of the lashings.
- Any cargo sitting on the side steel girders must be segregated by rubber, wood or similar anti-slip materials.
- The protruding dimensions should be protected and marked where the cargo is over height, length, and width.
- If the overall width, inclusive of packing, securing and lashing materials, does not exceed 2,438mm, the cargo will be treated as ‘in-gauge’ in width.
- If the overall length, including packing, securing and lashing materials, does not exceed 5,618 for 20′ FR and 11,652 mm for 40’FR, the cargo will be treated as ‘in-gauge’ in length.
- If the cargo’s overall height, including packing, securing, and lashing materials, does not exceed the height of the end posts when upright, therefore not impeding container stowage above will be treated as ‘in-gauge’ in height.
- Ends down flat rack will be treated as OOG.
ANNEX 1.
Preferred Lashing Methods
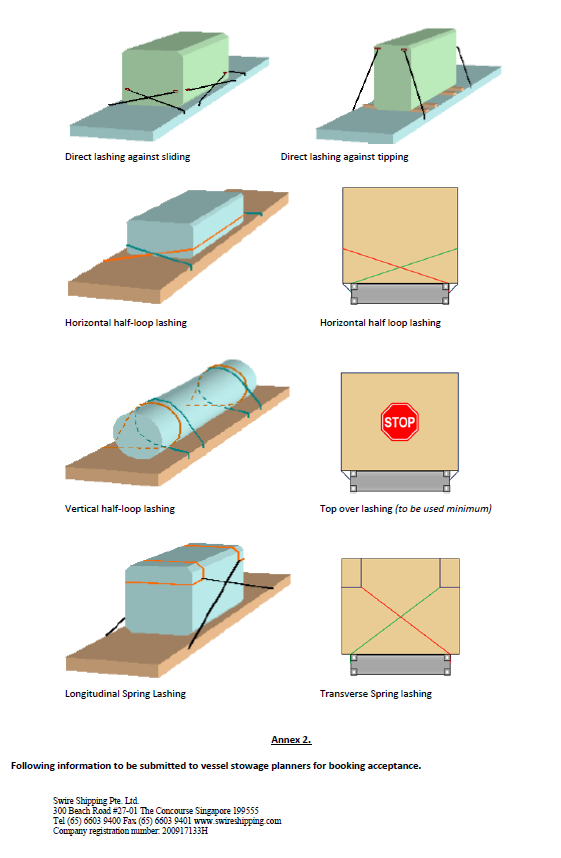
Annex 2.
Following information to be submitted to vessel stowage planners for booking acceptance.
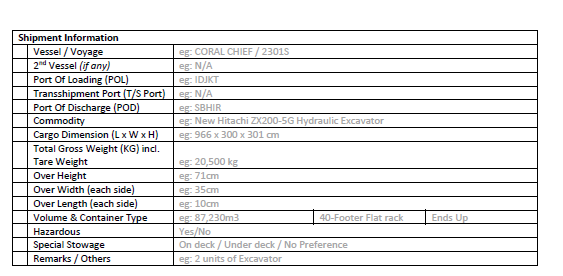
Please Note Below:
1. Attach cargo photos and lashing certificate.
2. Remarks: Include special handling requirements (if any)
3. OOG flatracks found insufficiently lashed shall be rejected prior to loading.
4. The cargo should be so arranged that its centre of gravity is closer to the mid-length and mid-width of the Flatrack container to avoid imbalance.
5. Cargo packed on the Flat rack must not obscure the top corner castings.
6. All in-gauge cargo must be stowed on flatracks with ends up.